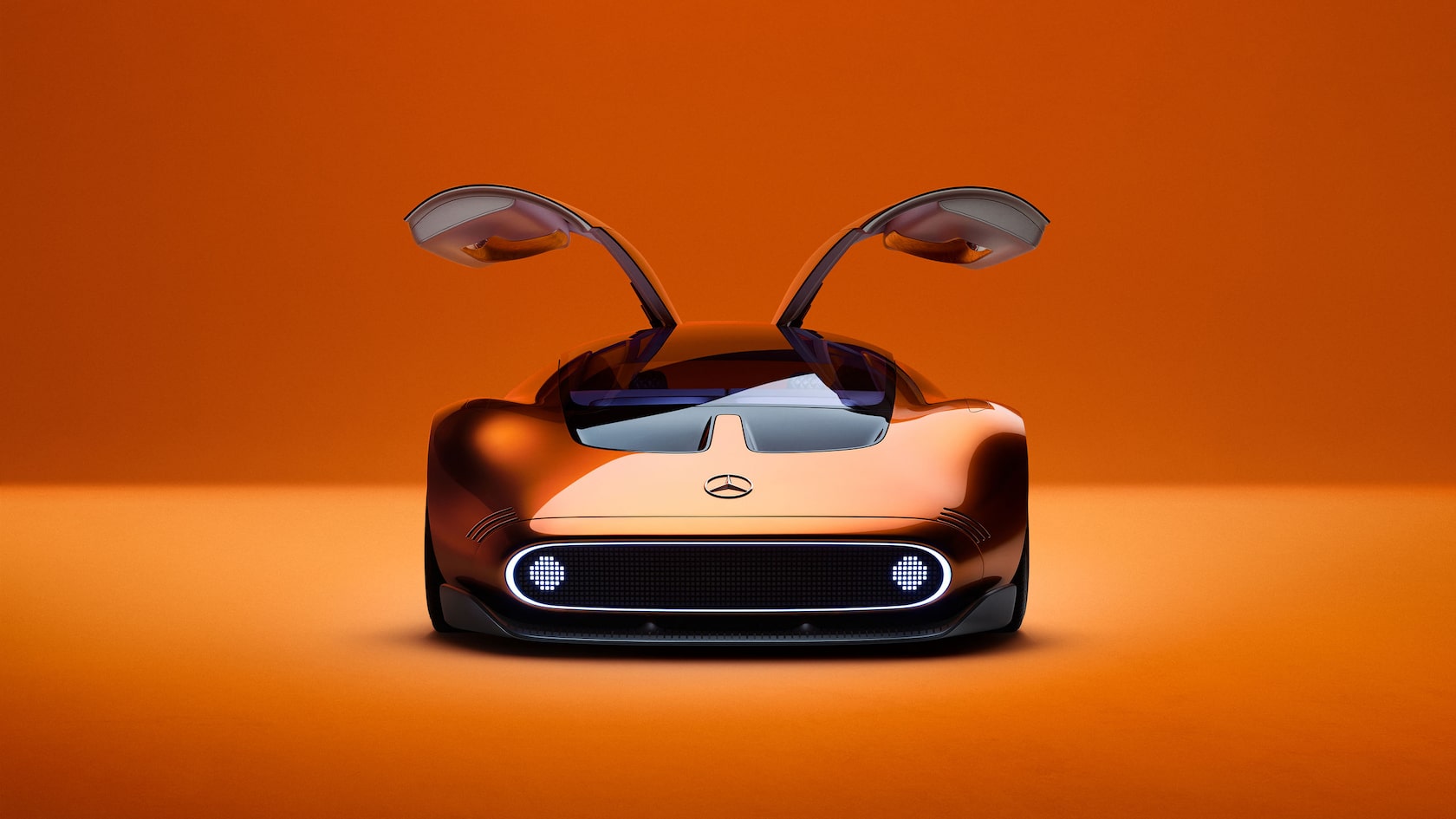
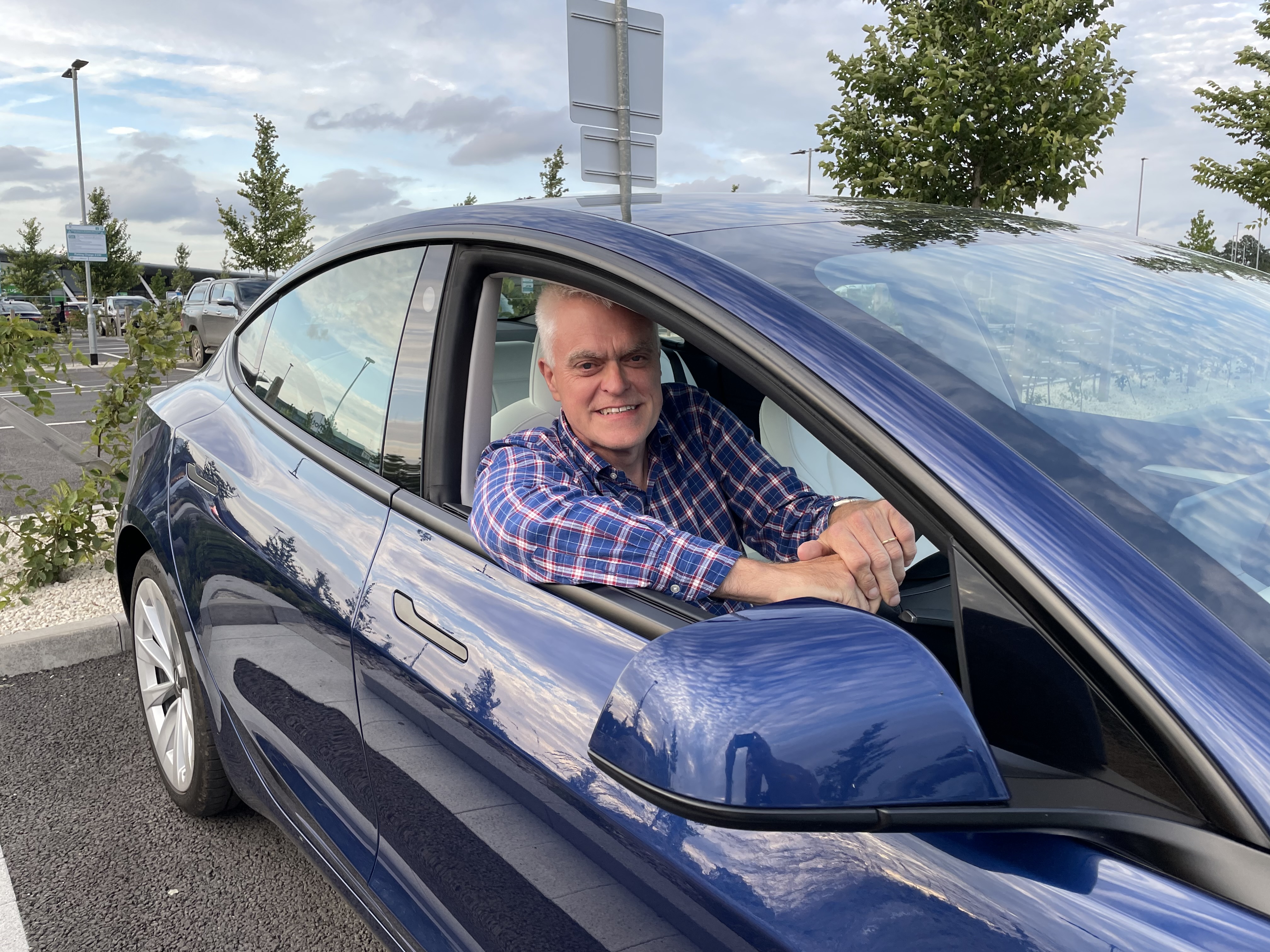
It’s common knowledge that electric cars have a weight problem. On average, they’re around 30% heavier than their combustion-engined equivalents, a burden that’s mainly down to the batteries. Manufacturers are working hard to eliminate this issue through developments like solid-state cells, new battery technologies, and more efficient packaging.
What’s less well-known is that there’s an equally furious battle going on to reduce the weight of the electric motors that turn the batteries’ energy into motion. Every part of the motor is being slimmed down. Rotor and stator laminations made out of steel sheets can be replaced by lighter and cheaper soft magnetic compounds produced by injection moulding.
Mild steel motor shafts can be switched to ones made from carbon-reinforced plastic and stainless steel. Motor windings can be lighter and more compact. On the face of it, this doesn’t look like a priority. Electric motors are normally lighter than the equivalent combustion engine – around 50kg as opposed to 200kg for the ones found in a typical small car. But there are still dividends in weight paring. Every little bit saved helps mitigate the weight of the batteries, reducing worries like the extra particulate pollution produced by heavier cars’ tyres and fears that old concrete car parks will collapse under the poundage of bloated EVs.
For me though, the biggest advantage of lighter and smaller motors is that they will find their way out from the body of the car, into its wheels. In-wheel motors have usually added too much unsprung weight, affecting ride and handling, and have not developed enough power. But those disadvantages are being overcome.
What can be achieved with in-wheel motors was demonstrated at CES 2024. The Hyundai Mobion, based on the Ioniq 5, uses the company’s e-Corner system, and has four hub-mounted motors. Freed from the constraints of driveshafts, all four wheels can swivel through 90 degrees. The car can crab sideways into parking spaces, spin on itself and steer diagonally from one lane to another.
As well as the tricks, the individual motors mean the car can control the torque sent to each wheel – this ‘vectoring’ helps the car corner, accelerate and brake more effectively. Wheel mounted motors also free up more space for supercapacitors in the body of the car that can help improve the regenerative brakes’ performance.
Chinese company Dongfeng launched production EVs with radial flux in-wheel motors last year. Radial flux motors are the cylinder-shaped ones normally found in electric cars but disc-shaped axial flux motors are intrinsically lighter and fit more easily into a wheel.
Sign up to the T3 newsletter for smarter living straight to your inbox
Get all the latest news, reviews, deals and buying guides on gorgeous tech, home and active products from the T3 experts
YASA motors in Oxford, owned by Mercedes-Benz, has created a 12kg axial motor that generates 250hp, and is engineering an “electric wheel motor and active suspension handling system” for Mercedes’ forthcoming Vision One-Eleven supercar. YASA aims to bring costs down so that Mercedes can use the system for all its cars.
We’re used to thinking of electric cars as conventional ones with electric power. But lighter, in-wheel motors have the ability to truly transform car architecture, in useful and exciting ways.
Jon is the main gadget reviewer and presenter for The Gadget Show on Channel Five. He was previously the Producer and Executive Producer of BBC's Top Gear between 1987 and 1999 and had a corner named after him on the Top Gear test track. He launched Fifth Gear for Channel Five and produced the show until 2004. When not presenting Jon enjoys writing. In 2019 Atlantic Books published his first book, Autopia: The Future of Cars, and he contributes regularly to Amateur Photographer magazine.